Autodesk Plant 3D vs Inventor: A Comprehensive Overview of DWG Workflows and Differences
Autodesk Plant 3D vs Inventor: A Comprehensive Overview of DWG Workflows and Differences
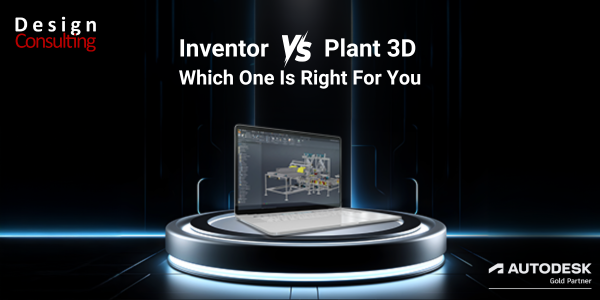
When it comes to CAD software, Autodesk offers a range of powerful tools tailored to specific industries. Two of the most popular among these are Autodesk Inventor and Plant 3D. Understanding the differences between these applications and their respective workflows is essential for professionals aiming to maximise their design efficiency.
This post provides a detailed comparison of Autodesk Inventor and Plant 3D, including a table that highlights their key differences, along with an in-depth analysis of their functionalities, workflows, and interoperability with other Autodesk tools.
Overview of Each Software
Inventor: Optimised for Small-Scale Mechanical Systems
Autodesk Inventor is ideal for projects involving detailed mechanical parts, assemblies, and compact systems. Its parametric 3D modelling capabilities allow engineers to create precise mechanical designs with intricate detail. The software’s tube and piping module is specifically designed for smaller piping projects, such as systems that can fit on the back of a truck.
However, while Inventor excels at mechanical design, it lacks built-in tools for process-specific tasks like P&ID creation. For projects that involve piping and instrumentation diagrams, users must create P&IDs manually, which can slow down the design process for larger, more complex systems.
Plant 3D: Designed for Large-Scale Process Plants
Autodesk Plant 3D is built for large, interconnected systems, particularly in industries like oil and gas, chemical processing, and water treatment. With its integrated AutoCAD P&ID tool, Plant 3D allows users to create P&IDs directly within the software. These P&IDs can be linked to 3D models, ensuring that any changes are reflected across the entire design, making the process more efficient and reducing the risk of errors.
Plant 3D also excels in plant-wide piping systems and isometric drawing generation essential for large-scale projects involving extensive piping runs and standardised equipment.
Key Differences Between Inventor and Plant 3D
The following table summarises the primary differences between Autodesk Inventor and Plant 3D:
Feature | Autodesk Inventor | Autodesk Plant 3D |
---|---|---|
Project Size | Small mechanical systems | Large plants, long pipe runs, extensive equipment layouts |
Piping Systems | Tube and Piping module for small-scale designs | Comprehensive plant-wide piping systems |
P&ID Integration | P&IDs must be created manually | AutoCAD P&ID integrated, linked to 3D models |
3D Equipment Modelling | Mechanical parts and compact assemblies | Plant-scale equipment and piping systems |
Interoperability | Export 3D equipment to DWG, integrate with Vault | Seamless catalogue management, isometrics generation |
Collaboration Tools | Autodesk Vault for version control | Integrated project management and collaboration tools |
Isometric Drawings | Not natively supported | Automatic generation from 3D models |
Material Management | Focused on mechanical parts and assemblies | BOM for piping and equipment management |
User Interface | Advanced 3D modelling environment | Intuitive interface for process design |
DWG Workflows in Inventor and Plant 3D
DWG Workflows in Inventor:
- File Creation: Users create 3D models in Inventor, which can be saved as DWG files for further editing in AutoCAD or for sharing with other stakeholders. This interoperability ensures that designs can be easily communicated and modified.
- 2D Drawings: Inventor allows users to generate detailed 2D drawings from 3D models, ensuring that all views, dimensions, and annotations are accurately represented in DWG format. This feature is crucial for manufacturing processes where precise specifications are required.
- Collaboration: The ability to export DWG files promotes collaboration with professionals who may not have access to Inventor but work within AutoCAD. This flexibility allows teams to work more efficiently, leveraging the strengths of each software.
DWG Workflows in Plant 3D:
- P&ID Development: Plant 3D users can create P&IDs, which are saved as DWG files, serving as the blueprint for piping and instrumentation layouts. This foundational step is essential for any plant design project, as it establishes the functional layout of systems.
- 3D Model Generation: The software allows users to create 3D models of piping systems and equipment that can be directly generated in DWG format. This feature streamlines the process of documentation and sharing, ensuring that all team members have access to the most up-to-date designs.
- Isometric Drawings: Plant 3D supports the automatic generation of isometric drawings from 3D models, which are essential for piping layouts. This capability not only saves time but also reduces errors that can occur when manually creating these drawings.
Interoperability With Advance Steel and AutoCAD
Both Autodesk Plant 3D and Inventor offer interoperability with Advance Steel and AutoCAD, enhancing their usability across different engineering disciplines.
- Advance Steel: While primarily for structural detailing, Advance Steel can take advantage of models created in Inventor and layouts from Plant 3D. This interoperability is beneficial for projects that require mechanical and structural components, enabling seamless integration of designs.
- AutoCAD: As the foundational software, AutoCAD serves as a common platform for DWG files. Both Inventor and Plant 3D can export to and import from AutoCAD, allowing seamless collaboration across various teams. This interoperability ensures that design updates are easily shared and implemented, promoting efficiency in the overall workflow.
Integrating Inventor with Plant 3D: The Power of BIM
For projects that require mechanical equipment design and plant-wide piping systems, Autodesk provides a robust solution through BIM content publishing tools. With these tools, engineers can design 3D equipment in Inventor and seamlessly integrate that content into Plant 3D.
This integration is particularly valuable for professionals working on multidisciplinary projects. For example, custom-designed mechanical equipment created in Inventor can be published as BIM content and incorporated into the Plant 3D catalogue ensuring consistency and eliminating the need for rework between platforms.
Real-world Applications
Understanding the differences between Autodesk Plant 3D and Inventor also involves examining their applications in real-world scenarios.
- Manufacturing and product design: In industries such as automotive and aerospace, Autodesk Inventor is widely used to design mechanical components. Engineers leverage their parametric modelling capabilities to create complex assemblies, conduct simulations, and manage changes efficiently. The ability to export detailed 2D drawings in DWG format allows for effective communication with manufacturing teams.
- Process Plant Design: For industries like oil and gas, water treatment, and chemical processing, Autodesk Plant 3D is the go-to solution. The ability to create detailed P&IDs, generate 3D models of piping systems, and automatically produce isometric drawings streamlines the design process. Collaboration tools enable multidisciplinary teams to work cohesively, ensuring that every aspect of the plant design is accounted for.
Experience the Difference Between Autodesk Plant 3D and Inventor
Both Autodesk Inventor and Plant 3D are powerful tools, each designed for specific industries and applications. Inventor excels in mechanical design and manufacturing, while Plant 3D focuses on process and plant design. The choice between these two software options largely depends on the industry, project requirements, and desired workflows.
Understanding the differences in their DWG workflows, interoperability with other Autodesk products, and unique features is crucial for professionals aiming to enhance their design processes. By leveraging the strengths of each application, users can ensure that their designs are efficient, accurate, and tailored to their specific needs. Whether you are involved in mechanical design or plant engineering, choosing the right software is essential for success in today’s competitive landscape.
Contact Us
Contact us to find out how we can help your business. Fill out the form below, by live chat, phone or email.
P: 1800 490 514 | E: [email protected]
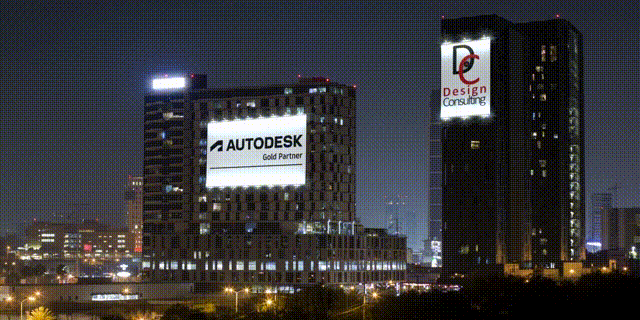
