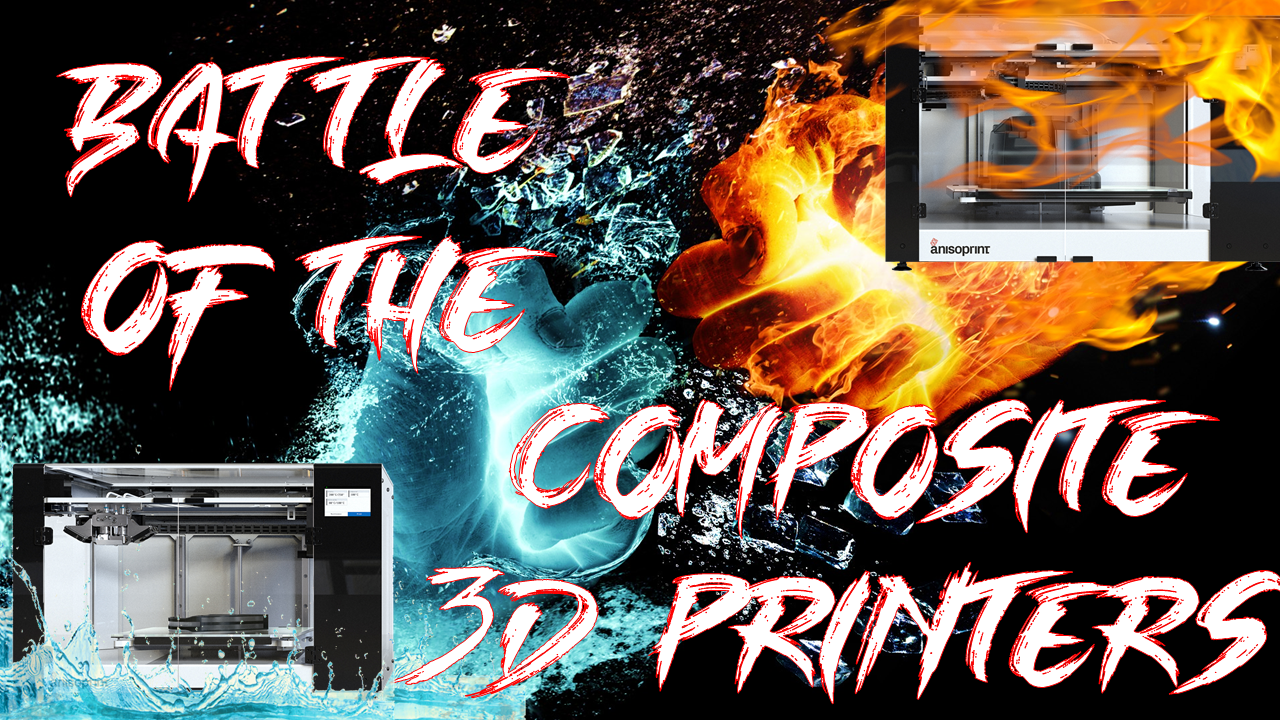
3D Printer Review: Battle of Continuous Fiber Composites
With so many choices for 3D printers on the market, few can deliver strength-to-weight ratios like continuous fiber 3D printers.
Using FDM Fused Deposition Modeling (aka FFF) technology, these 3D printers lay continuous fibers into the base filament of the 3D printed part to produce strong lightweight parts that rival metal.
There is a couple of competitors in the market and Anisoprint with over 10 years of composite manufacturing experience offering a clear alternative to the rest.
The name Anisoprint is derived from anisotropy, to exhibit different parameters of stiffness and strength in different directions (e.g. horizontal and vertical).
Understanding the differences between Anisoprint and their main competitors can be confusing, however, understanding how traditional composite fiber parts are manufactured gives you insight into how these manufacturing processes were adapted to 3D printing technology.
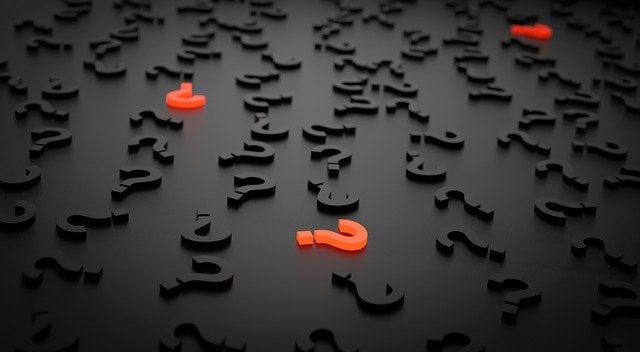
Composite Manufacturing
Without getting too technical, producing composite parts is laying in fiber, such as carbon fiber, into polymer matrix layer by layer and laminating them together: and it is the way these 3D Printers laminate that is the most distinguishing characteristic between them.
The type of fiber and the volume of fiber in a composite can vary, for instance, when manufacturing aerospace composites the amount is as high as 60%.
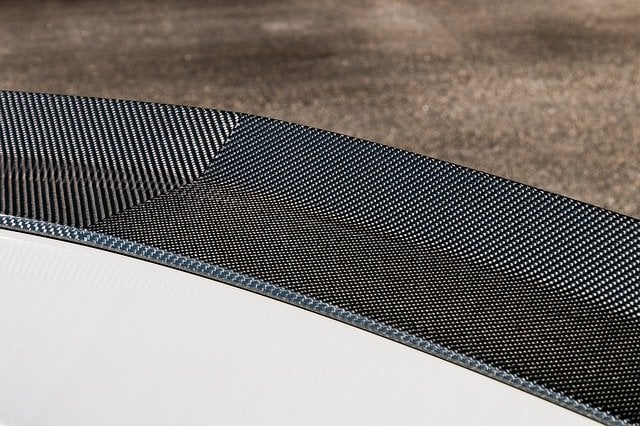
3D Printer Fiber Extrusion Methods
Both Anisoprint and the competition use a dual extrusion technique where there is a base filament and continuous fiber, the latter can be customized in the slicing software.
The way the competitor system extrudes the fiber is a prepreg placement technique: heating a roll of filament fiber which has about 28% fiber and the remaining being a thermoplastic and by heating the filament as it extrudes, it bonds to the base thermoplastic filament, usually a Nylon or Nylon mixed with short fibers of carbon fiber and limited colour choices.
Anisoprint use a unique co-extrusion technique, where prepreg (fiber impregnated with thermoset) and thermoplastic matrix and fed into the extruder simultaneously. The extruder heats them, making the matrix soft and elastic and the fiber sticky and less rigid, then the blend is extruded as one single composite material.
Its this patented co-extrusion technique using preimpregnated (with thermoset) fiber that gives it the ability to bond to a wide range of thermoplastics.
Composite Co-Extrusion
The benefit of using Anisoprint co-extrusion is adaptive 3D printing: where the volume ratio change or amount of matrix and fiber can be modified, if required.
Anisoprint co-extrusion allows 3D printer users to create parts with fiber volumes up to 60% (which meets the demands of aerospace production), 3D print internal lattice structures with continuous fiber (not just base filament), make use of adaptive layer thickness, and make many other flexible choices to lay continuous fiber.
Using prepreg plus thermoplastic instead of dry fiber plus thermoplastic creates an open system, giving the user the ability to print with any type of base filament or colour within the specifications of the printer, such as PLA, Nylon, TPU, ABS, Pet-G, or composites such as a thermoplastic with short fibers to provide characteristics for specific applications and conditions, such as high or low temperature, friction, UV, chemical resistance, anti-microbial/bacterial or flame retardant.
Materials
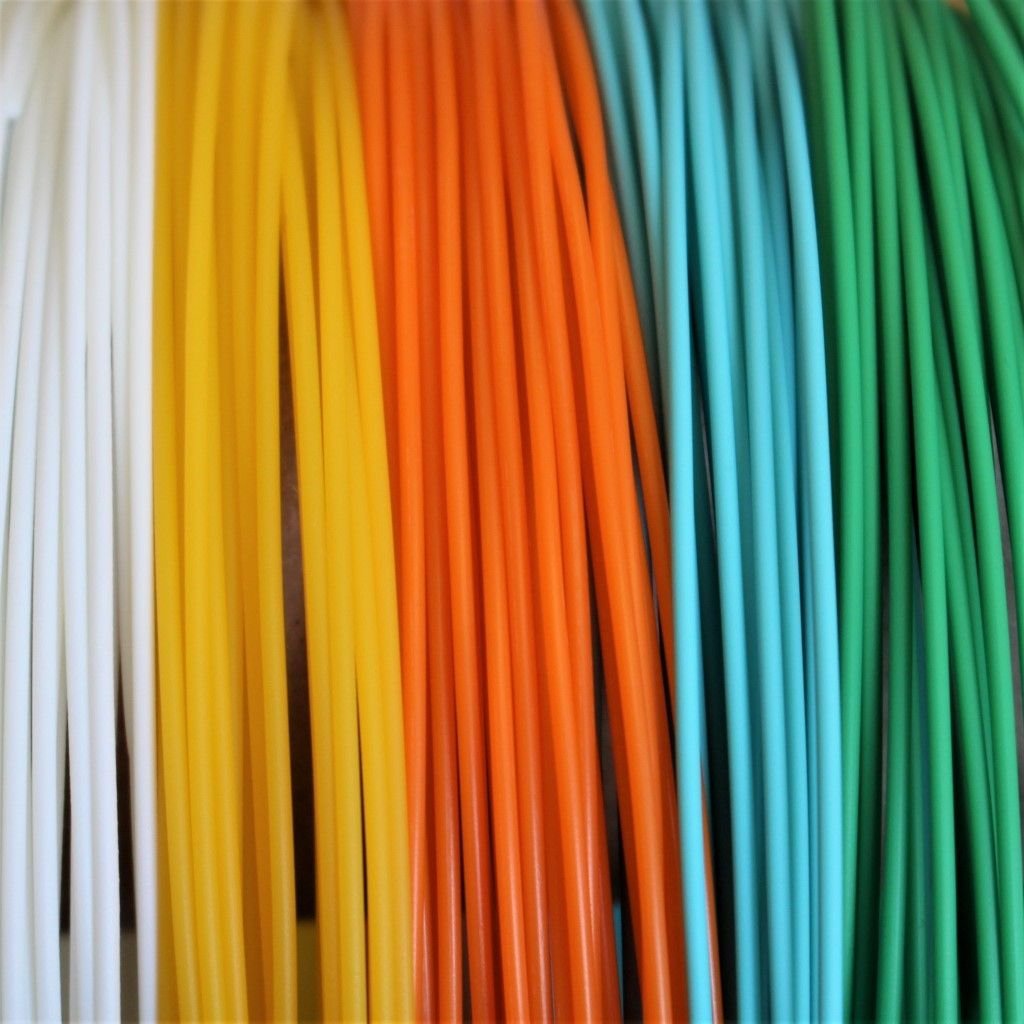
Many other continuous fiber 3D printer manufacturers offer only a limited range of their proprietary materials which can be limited to the application and colour selection. While Anisoprint have their own materials as well, they offer an open system, so users have a wide range for choice when it comes to material applications such as Nylon, PLA, PET-G, Polycarbonate, PC-FR, TPU, etc. and of course any colour choice that the filament comes in, so you can print in the right material for the right application.
Aura Slicing Software
Aura slicing software allows the user to use the flexibility of anisoprinting technology to the fullest. With a wide range of adjustable parameters that are unique in the market, Aura can fully control the process of printing to meet all customer demands. For those who wish to simply choose a material and print, there is a number of preset optimized plug and play profiles for various materials that can produce an excellent finished part with no manual input or parameter adjustment.
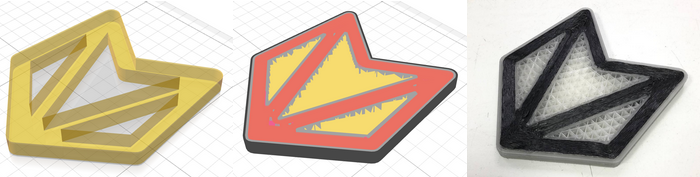
Masking
A mask is an additional model that is added to the work area to intersect with the base model, changing the model’s internal structure in the intersection volume.
This type of marking intersection serves for adjusting fiber and support parameters that are different from those selected for the rest of the model.
You can see the base model (grey) and the mask model (orange) in the picture below. The base part volume inside the mask will be printed with special settings for the mask.
Layer Thickness
Aura software allows users to adapt layer thickness, for instance, a user may want a nice surface finish and 3D print a layer of 50um around the surfaces and on the inside 3D print 200um or higher where surface finish is not an issue, this hack increases the speed of the print.
Fiber Directions
Competitors’ slicing software has the option for linear or concentric printing of continuous fibers.
Anisoprint Aura software gives the user the option for a combination of:
- Linear
- Concentric (with an option to choose separately, concentric fibers for inner and outer perimeters)
- Curvilinear trajectories
- Lattices
These combinations provide users with the flexibility to lay fibers in the right directions giving maximum strength and directional force.
Lattices
The ability to 3D print various lattice structures with continuous fiber gives parts strength in the right places, speed to print and lighter parts, providing load distribution along the 1D ribs, making the part 2-3x stronger compared to the one with plastic lattices. Compared to printing on a competitor’s machine that cannot print continuous fiber lattices such part will also be lighter.
Anisoprint provides users with flexible options for lattice patterns:
- Solid
- Rhombic
- Isogrid
- anisogrid
Fiber printing (Microns)
Aura allows 3D printing of continuous fibers of up to 350um whereas the competing 3D printing systems only 3D print up to 200um.
Industrial Continuous Fiber Composite 3D Printers
When it comes to industrial application, Anisoprint has a true industrial printer with industrial level components, designed for 24/7 production to print 60cc p/hr of continuous carbon fiber with a max travel speed of 20,000 mm per minute:
- PLC Based BOSCH Rexroth XM42 controller
- Servo motors with brakes
- Industrial automation
- Safety and sensors
- Liquid cooling
- 400 degrees max. extruder temp to 3D print thermoplastics such as PEEK and PEI
- 160-degree heated chamber
- Build volume: 600x420x300mm
- Tool changer for 4 extruders
- Material dryer
- Server-based software
Competitive Comparison Matrix - Continuous Fiber 3D Printers
Anisoprint Desktop Composer | Competitor Desktop | |
---|---|---|
Build Volume | A4: 297x210x140mm - 25% larger build volume than competitor A3: 460x297x210mm - 77% larger build volume than competitor | 320x132x154mm |
Base Filaments (Matrix) | ||
Open material system | Yes | No |
Continuous Fibers | ||
Continuous carbon fiber | Yes | Yes |
Continuous basalt fiber | Yes | No |
Continuous aramid fiber | No | Yes |
Continuous fibreglass fiber | No | Yes |
Variable Fiber to Volume Ratio | Yes | No |
Fiber to volume Ratio | Up to 60% | 28% |
Layer Resolution | ||
Resolution (microns) | 36 to 360 | 100 to 200 |
Adaptive Layer Resolution | Yes | No |
Continuous Fiber Directions | ||
Linear Trajectories | Yes | Yes |
Concentric Trajectories | Yes | Yes |
Rhombic Lattice Structures | Yes | No |
Isogrid Lattice Structures | Yes | No |
Anisogrid Lattice Structures | Yes | No |
Curvlinear Trajectories | Yes | No |
Combination of Trajectories | Yes | No |
Combination of Linear, Curvlinear, and Concentric Trajectories | Yes | No |
Combination of Trajectories and Lattices | Yes | No |
Slicing Software | ||
Masks | Yes | No |
Support Blockers | Yes | No |
Support Enforcer | Yes | No |
Headless Mode (CLI) | Yes | No |
Export G-Code | Yes | No |
Anisoprint Industrial Prom IS 500 | Competitor Industrial | |
---|---|---|
Build Volume | 600x420x300 - 78% larger build volume than competitor | 330x270x200mm |
Servo Motors | Yes | No |
Tool Changer | Yes | No |
Base Filament Extruders | 4 | 1 |
Liquid Cooled Extruder | Yes | No |
Max temperature of 400 degrees | Yes | No |
Heated Build Chamber | Yes | No |
Material Dryer | Yes | No |
Safety Sensors | Yes | No |
Laser Scanning | No | Yes |
Base Filaments (Matrix) | ||
Open material system | Yes | No |
Continuous Fibers | ||
Continuous carbon fiber | Yes | Yes |
Continuous basalt fiber | Yes | No |
Continuous kevlar fiber | No | Yes |
Continuous fibreglass fiber | No | Yes |
Variable Fiber to Volume Ratio | Yes | No |
Fiber to volume Ratio | Up to 60% | 28% |
Layer Resolution | ||
Resolution (microns) | 60 to 350 | 50 to 200 |
Adaptive Layer Resolution | Yes | No |
Continuous Fiber Directions | ||
Linear Trajectories | Yes | Yes |
Concentric Trajectories | Yes | Yes |
Rhombic Lattice Structures | Yes | No |
Isogrid Lattice Structures | Yes | No |
Anisogrid Lattice Structures | Yes | No |
Curvlinear Trajectories | Yes | No |
Combination of Trajectories | Yes | No |
Combination of Linear, Curvlinear, and Concentric Trajectories | Yes | No |
Combination of Trajectories and Lattices | Yes | No |
Slicing Software | ||
Masks | Yes | No |
Support Blockers | Yes | No |
Support Enforcer | Yes | No |
Headless Mode (CLI) | Yes | No |
Export G-Code | Yes | No |
Conclusion
While on the surface, composite 3D printers seem to be the same and do similar functions, when you look at the extrusion hardware and slicing software in the desktop range and the motors and other components in the industrial range, differences are quite contrast.
If you are looking for greater continuous fiber choices, then Anisoprint may not be the right fit, however, the fact that it can use any base plastic, whether it be rigid or flexible, offers greater choice and eliminates the need for a wider range of continuous fiber.
The Anisoprinting system gives the user basic settings like the competition to simply print and go, or for advanced use, the freedom and the ability to manipulate the direction of fibers, lattice structures to produce lighter parts and the choice in the right base filament to fit the desired application with a bigger build volume to print larger parts.
In the industrial range, the Prom is a true industrial size and built for 24×7 use with 4x tool changers and servi motors, while the alternative is small and doesn’t use the same industrial components but compensates with a laser scanning tool.
All composite 3D printers with continuous fiber will give you strong, lightweight parts that rival replacing metal, it’s just that the Anisoprint has the hardware and software to be to steer the continuous fibers with greater flexibility, which caters to the benefits of composite fiber manufacturing.
Contact Us
If you would learn more about Anisoprint, please contact us by calling on 1800 490 514, by filling out the form or clicking the live chat in the bottom right-hand corner.
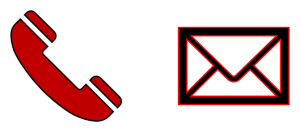