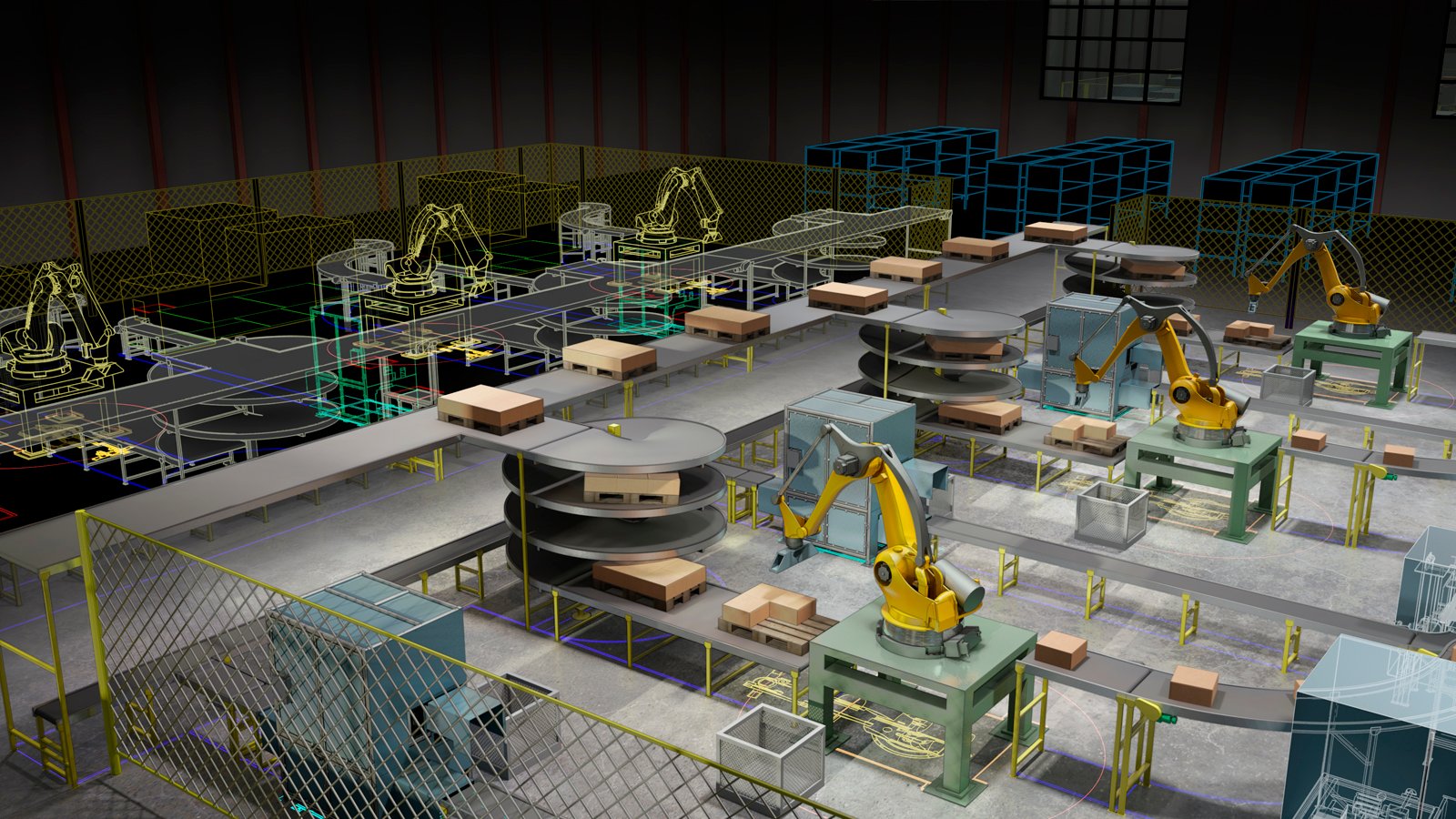
The Foundation of Factory Design Suite
Part 1 summarised the challenges and some of the tools used in designing and managing a Factory/Facility. This part focuses on Autodesk’s solution that addresses these challenges and subsequent posts will cover working with existing layouts, creating new layouts, analysis (process analysis, machine utilisation & energy consumption), visualisation and linking Factory Design Suite with external programs and databases. Back to the solution, in this case, we’ll focus on the midrange solution, Factory Design Suite Premium (FDS-P) because it has Inventor, so I’d like to focus on the 3D Parametric and other design features Inventor has.
FDS-P utilises 2 Software programs at the core, AutoCAD (with the Mechanical, Architecture Add-Ons) and Inventor with Autodesk Factory Design Utilities linking them together.
With these programs you can layout your facility using AutoCAD or Inventor as you normally would using CAD but by using the Factory Design Utilities you can design and analyse your Facility better and faster. The utilities have tools to create a factory layout grid to work in, add overlays and manage AutoCAD layers (Inventor) and you can bring in point cloud data from 3D Scans or Photos using ReCap Photo of an existing facility and place it over the grid.
You can use conventional design tools to create your facility, but by using the Asset Library, you drag and drop factory assets onto your grid (or create new assets), insert 3D models from the most the popular CAD formats (and publish these as assets) or publish assets from 2D AutoCAD blocks.
[youtube http://www.youtube.com/watch?v=kVpkiDnTb3E&w=640&h=390]Factory assets snap together like leggo, with tools to define relationships such as constraints, landing surface, alignment and replacing one asset with another. The asset library is constantly updated, you can add to the library and create chain assets instead of dragging and dropping assets in one by one. You can also tag your assets, manage the visibility and search for assets based on their annotation within the modeling environment.
The Factory Design Utilities has a synchronise function between AutoCAD & Inventor, so any designs or changes made in AutoCAD will update in Inventor and vice/versa. So if you dropped in a conveyor system asset in AutoCAD, you would see the top view of the 3D model. You can now switch to Inventor and work on the Z Axis, see the model in 3D and design the conveyor so it goes up and over a platform.
The analysis tools that come with Factory Design Utilities work in AutoCAD under the Material Flow section where you can import XML or Excel Data or define parameters to analyse processes to reduce or eliminate bottlenecks, analyse machine utilisation or energy consumption.
Additional programs included in FDS-P are for Reverse Engineering, Visualisation, Analysis & Data Management.
For Reverse Engineering, AutoCAD Raster Design is for raster to vector conversion to convert scanned images or digital documents like PDF into a useable vector document in CAD so you can re-use the data, dimension and add to the existing design. ReCap is to import, process, clean up and edit point cloud data. AutoCAD & Inventor opens point cloud data, ReCap will let you process the data in the cloud and edit it before you bring it in.
Visualisation Tools are Showcase for Photo Realistic Flat Images and Animations (Check out this review for more info), 3ds Max Design for Cinematic Quality visualisation and Navisworks which can also be used for visualisation too.
If you have a large project and need to communicate with internal & external stake-holders, you can’t go past Navisworks. Navisworks Simulate does 2 main things; Project/Model Viewing and Simulation & Analysis. It will open almost any CAD file or point cloud data, where you can assemble these CAD files if required or open your existing 3D Factory Layout, collaborate with team members, have real-time navigation of your Factory with tools for 5D Project Scheduling for quantity take-off & estimating.
It’s animation capabilities provide photo-realistic rendering where you can animate the sequence or deconstruction of your model or animate components like doors, gates, machinery, conveyors, etc. in a walk-through scene. These animation capabilities also tie-in with 5D Project Scheduling so you can visualise the construction of your facility and do budget estimations. Navisworks Manage (in FDS-Ultimate), goes further, identifying and managing clashes and interferences. This overlaps with Inventor, however, if you’re bringing in other CAD files into Navisworks and connecting the dots, it’s a handy tool.
Finally, FDS comes with Vault Basic, which provides Data Management to securely protect data, manage and administer the data properly, view 3D models and reference files, find files based on any metadata, version control and integrate with MS Office documents. Anything more than that will need higher versions of Vault.
Adopting new technology to increase productivity is always a great idea however, licensing costs, learning a new system, legacy data and being able to link into other applications that overlap should also be addressed too, so I’ll continue onto this common area of concern to see how you can transition from an existing system rather than showing you wizz-bang features that will soon fizzle out if the pain outweighs the gain.