Rize – World’s first UL Greenguard 2904 Certified 3D Printers
Rize - World's first UL Greenguard 2904 Certified 3D Printers
How safe is your 3D printer for indoor use and what is the air quality while it is in use?
Studies have found that 3D printers in indoor settings pose potential health threats to those exposed to the nano-sized ultrafine particles (UFPs) that come off the printer during operation.
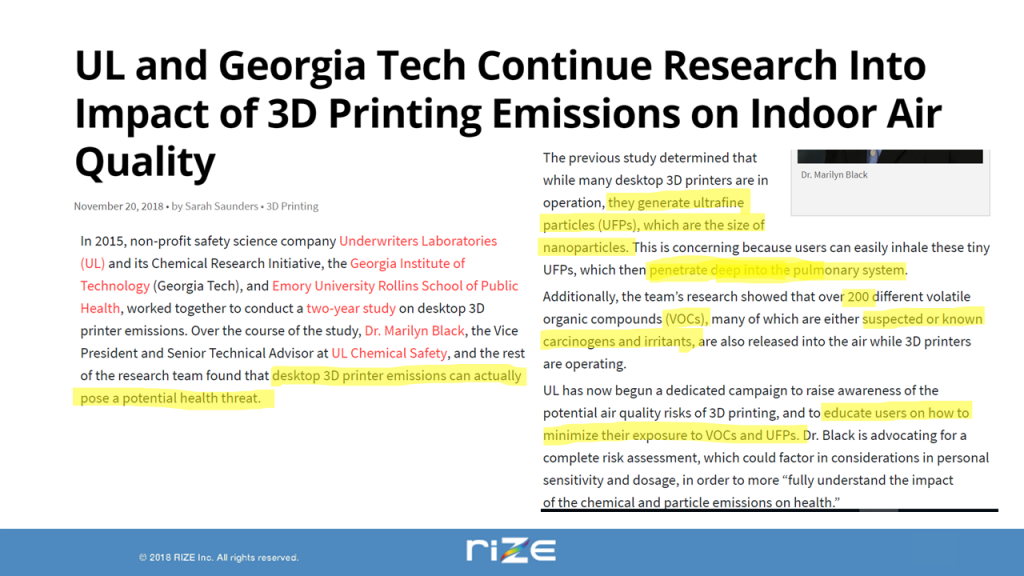
UL Greenguard 2904 Certification
Underwriter Laboratories (UL), the world’s leading non-profit safety science organization, has announced a new standard UL 2904 for safety in 3D printing focusing on setting standards for indoor air pollution by 3D Printers.
This certification assures users that the 3D printer meets the safety and sustainability goals in LEED certification, Zero Waste.
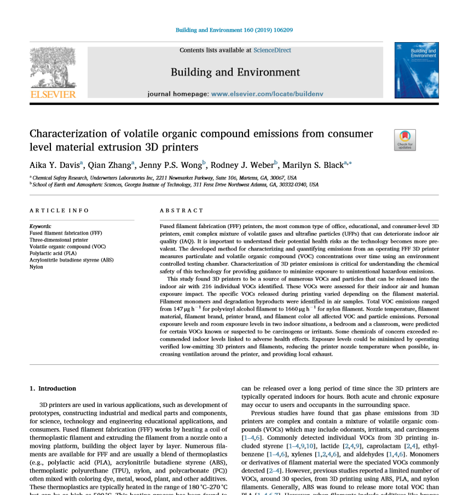
Carcinogens in 3D Printer Extrusion
RIZE became the first company in the world to receive UL 2904 GREENGUARD certification for RIZE 2XC Printing system – Rize 2XC Printer, RIZIUM Composite Filament. Rize met and exceeded the certification requirements to receive the certification of UL Greenguard.
More than 90% of the particles emitted by 3DPrinters are in nanoparticle range (less than .1 micron) and when inhaled can cause cardiovascular and pulmonary issues.
There are 200+ VOC’s detected, many are known irritants and carcinogens:
- Formaldehyde (known carcinogen)
- Styrene (flammable chemical and irritant)
- Caprolactam (known irritant of eyes, throat and headaches)
- And many others
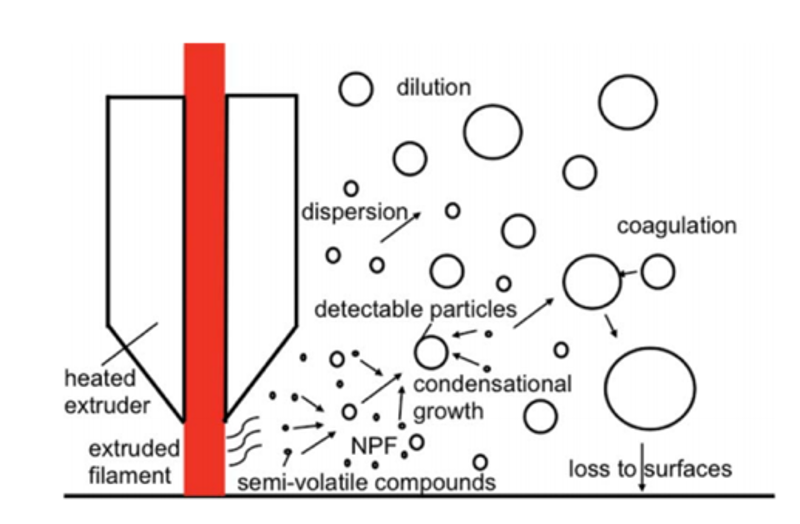
Safe 3D Printers for Office, Education and Hospital Use
Many consumers take the risk with 3D printing unaware of the health issues and businesses with industrial floorspace can have 3D printers in well-ventilated environments, however, in office environments and education where there are small children and in hospitals where there are sick and elderly, these risks and liabilities become issues when 3D printers produce poor health quality.
Having a UL 2904 certified 3D printer reduces the risk, liability and long-term health implications of using 3D printers in indoor environments.
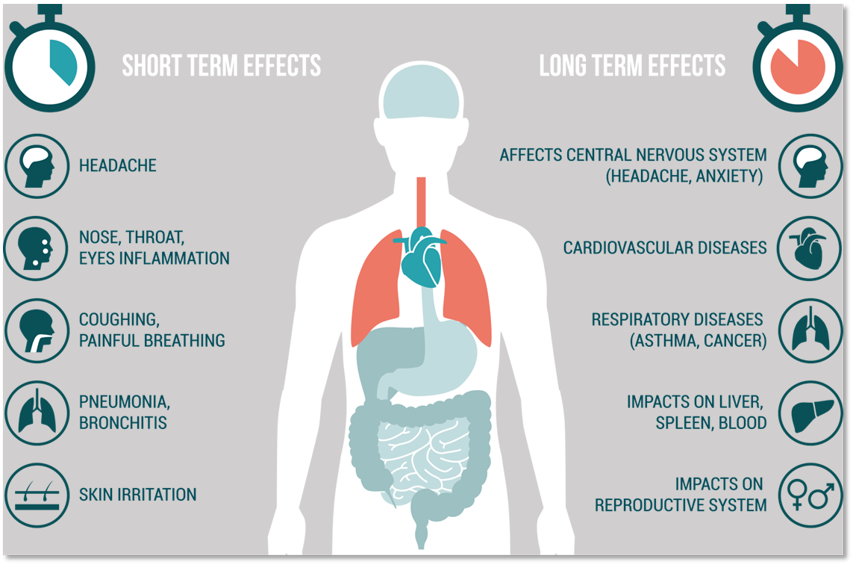
Rize 3D Printers - The Safest Choice
If it is safety first when choosing a 3D printer, then Rize composite and full colour 3D printers are the leading choice for environments where air quality and the short and long term side effects of carcinogen exposure are primary factors.

Contact Us
If you would to discuss Rize 3D printers, please contact us by calling on 1800 490 514, by filling out the form or clicking the live chat in the bottom right-hand corner.
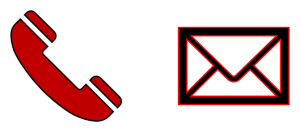