Automate your Design Processes with Autodesk Vault
5 Powerful Ways to Automate your Design Processes with Autodesk Vault
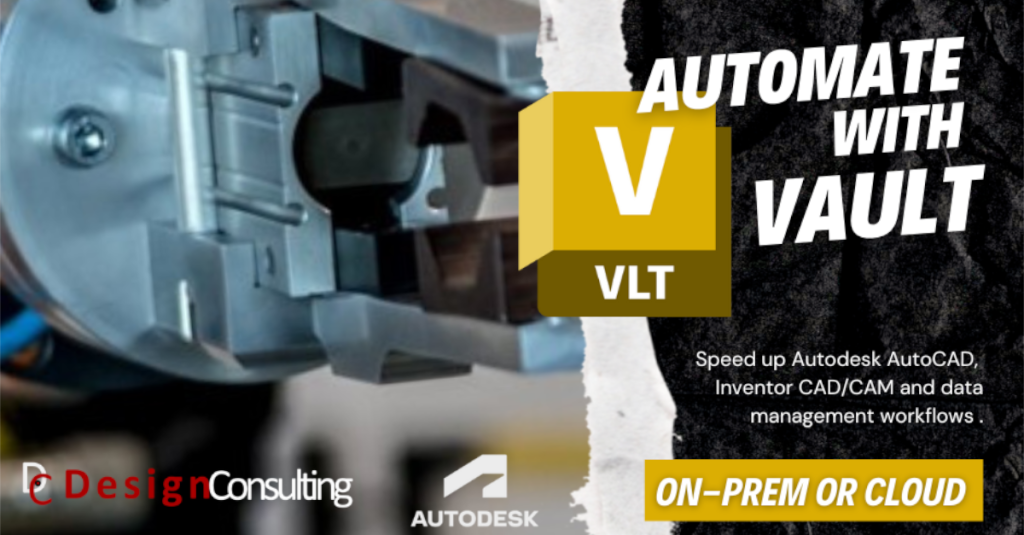
Design automation is the use of software to automate repetitive tasks in the design process. This can save time and money by freeing up engineers to focus on more creative and strategic work. Autodesk Vault is a product data management (PDM) software that includes a number of features for design automation.
Autodesk Vault is available on-premise or on cloud
Benefits of design automation in Autodesk Vault
Design automation in Autodesk Vault can also provide a number of other benefits, including:
- Increased accuracy: By automating repetitive tasks, engineers can reduce the risk of errors.
- Improved efficiency: Engineers can spend more time on creative and strategic work, and less time on administrative tasks.
- Improved collaboration: Autodesk Vault can help engineers to collaborate more effectively by providing a central repository for design data.
- Improved compliance: Autodesk Vault can help organizations to comply with industry regulations by providing a secure and auditable way to store design data.
If you are looking for ways to save time and money in your design process, then design automation in Autodesk Vault is a great option. By automating repetitive tasks, you can free up your engineers to focus on more creative and strategic work. This can lead to increased accuracy, efficiency, collaboration, and compliance.
Copy Design
One of the most common tasks in the design process is copying existing designs. This can be a time-consuming and error-prone process. Automate the copy design process by creating a new design that is a copy of an existing design. This can be done with a single click of a button.
Automatic Numbering Schemes
Another common task in the design process is assigning part numbers to parts. This can also be a time-consuming and error-prone process. Automate the part numbering process by creating a custom numbering scheme. This can ensure that part numbers are assigned consistently and correctly.
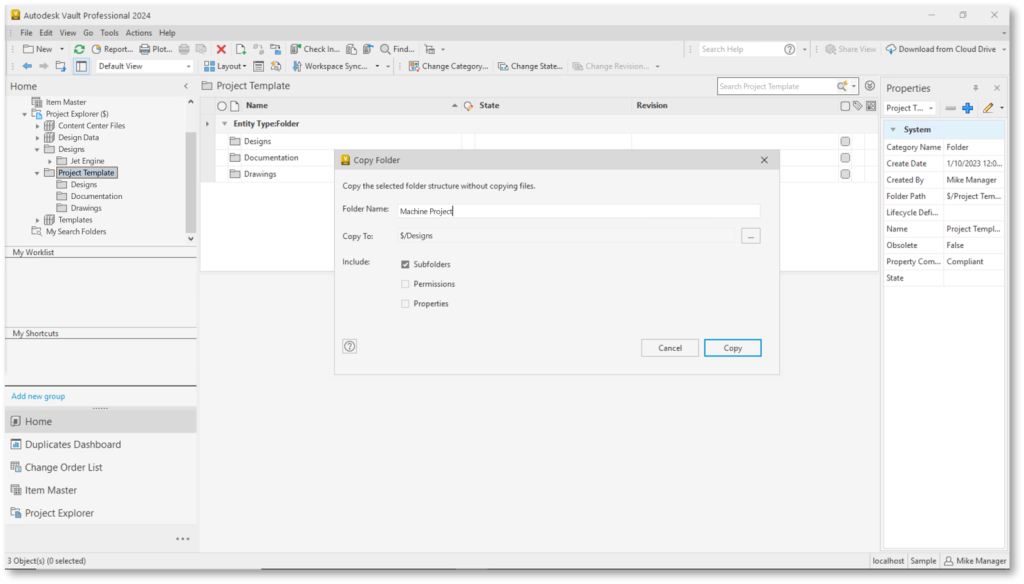
Revision Control
As designs evolve, it is important to track changes. Automate the revision control process by creating a revision history for each design. This can help engineers to track changes and to revert to previous versions of designs if necessary.
Version Control
In addition to revision control, Autodesk Vault can also automate the version control process. This means that multiple versions of a design can be stored in Vault and that changes can be tracked between versions. This can help engineers to collaborate on designs and to track the progress of designs over time.
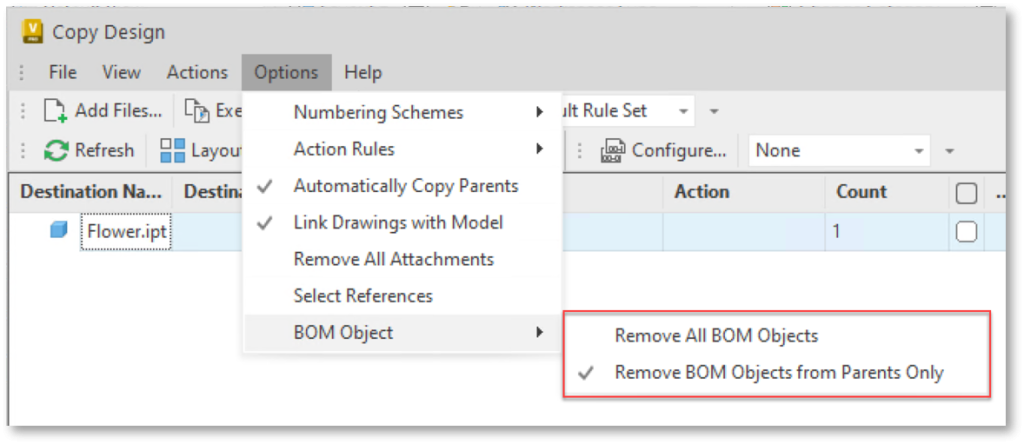
Job Processor
The Job Processor is a powerful tool that can be used to automate a variety of design tasks. This includes tasks such as generating bills of materials, creating drawings, and submitting designs for manufacturing. The Job Processor can be used to automate repetitive tasks, freeing up engineers to focus on more creative and strategic work.
JP Pro is a power job processor built on Autodesk Vault Professional that allows you to automate publishing of files, email notifications, synchronisation and much more..
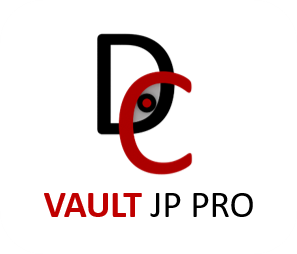
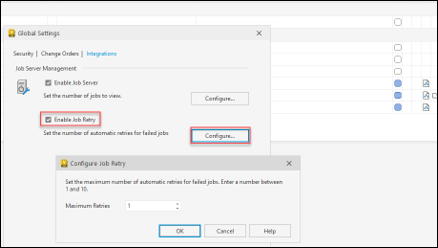
ERP Integration
In addition to the 5 ways to automate using Vault, Vault can be integrated with a variety of enterprise resource planning (ERP) systems. This allows engineers to share data with other departments in the organization, such as manufacturing and sales. This can help to improve communication and collaboration between departments, and to ensure that everyone is working with the latest information.
Ready to Automate?
Design automation is a powerful tool that can save time and money for AutoCAD and Inventor users. Autodesk Vault includes a number of features for design automation, including copy design automation, automatic numbering schemes, revision control, version control, job processor and ERP integration. These features can help engineers to automate repetitive tasks, freeing up time for more creative and strategic work.
Contact us on 1800 490 514, [email protected] or fill out the contact us form below.